In a world where everything moves at lightning speed, resting on your laurels is not an option!
To stay ahead, companies must constantly optimize their processes, enhance their efficiency, and better satisfy their customers. Whether you’re a start-up looking to structure your methodology, an SME seeking greater efficiency, or a large corporation aiming to mobilize its teams, there are strategies and tools tailored to every need!
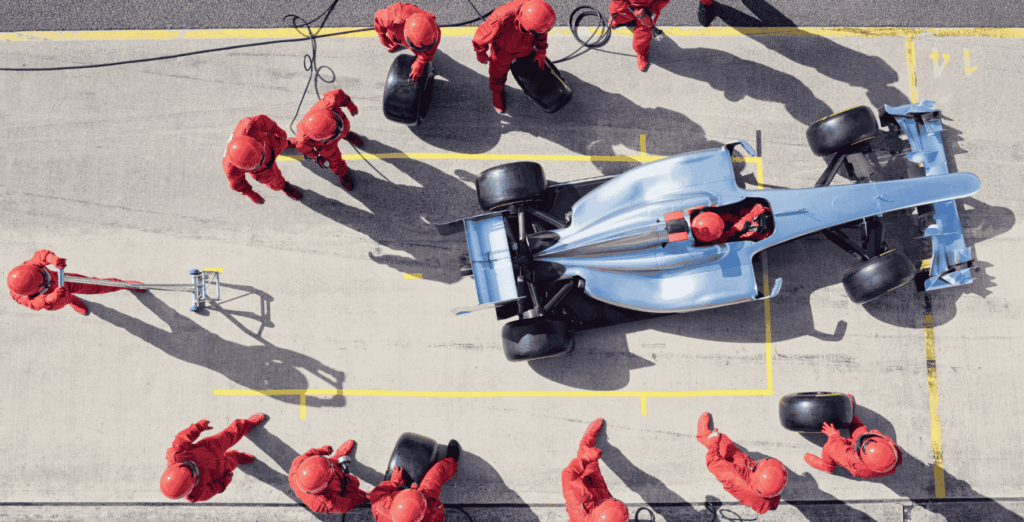
The Main Continuous Improvement Methods
Kaizen: The Power of Small, Ongoing Improvements
“Kaizen 改善”, meaning “change for the better” in Japanese, is more than just a methodology, it’s a mindset. The idea? Instead of aiming for big revolutions, focus on small, daily improvements that, over time, create significant impact.
How does it work?
- Identify small, everyday problems.
- Implement simple and quick solutions.
- Involve all employees in the improvement process.
Advantages of Kaizen
- Easy to implement, even in small businesses.
- Encourages collective intelligence and team engagement.
- Supports gradual change, making it less disruptive.
Limits of Kaizen
- Requires long-term commitment.
- Less effective for major transformations that demand complete process overhauls.
Kanban: Visualize to Optimize
“Kanban 看板” is the go-to method for teams that want clear visibility over their tasks and projects. Popularized by Toyota, this system uses visual management with boards and cards to track workflow progress efficiently.
How does it work?
- A board with columns representing different process stages
(e.g., To Do → In Progress → Done). - Cards for each task that move through the stages as work progresses.
- A limit on tasks in progress to avoid bottlenecks.
Advantages of Kanban
- Offers a clear and instant view of ongoing work.
- Reduces multitasking and enhances workflow efficiency.
- Simple to set up.
Limits of Kanban
- Not ideal for projects requiring strict, detailed tracking.
- Can become overly complex if poorly structured.
Lean Management: Eliminate Waste to Maximize Value
“Lean Management” is built on a simple idea: minimize wasted time, energy, and resources to focus only on what adds value.
How does it work?
- Define value: identify what truly matters to the customer or user.
- Eliminate waste (Muda): cut unnecessary steps, reduce excess inventory, avoid production errors.
- Optimize workflows for better efficiency.
Advantages of Lean
- Cuts costs and lead times.
- Improves product and service quality.
- Adapts well to customer needs.
Limits of Lean
- Difficult to implement without a true culture of continuous improvement.
Did you know? Amazon applies Lean principles to optimize its supply chain and reduce time between order and delivery! |
Six Sigma: Data-Driven Excellence
“Six Sigma” is a highly structured method that uses statistics and data analysis to reduce defects and improve process quality. The goal? Less than 3.4 defects per million units produced.
How does it work?
- Analyze processes to detect variations and sources of error.
- Implement a structured action plan, often using DMAIC
(Define, Measure, Analyze, Improve, Control). - Monitor performance to ensure continuous improvement.
Advantages of Six Sigma
- Relies on measurable, reliable data.
- Drastically reduces errors and defect-related costs.
- Ideal for large industrial firms and services requiring top-tier quality.
Limits of Six Sigma
- Heavy and complex to deploy.
- Requires specialized training and data analysis expertise.
PDCA: The 4-Step Continuous Improvement Cycle
The “PDCA cycle (Plan-Do-Check-Act)”, also known as the Deming Wheel, is a simple yet highly effective method to test improvements, adjust them, and integrate them sustainably.
How does it work?
- Plan: identify a problem or a root cause and propose a solution.
- Do: test the solution on a small scale.
- Check: measure the results.
- Act: roll out the improvement if successful.
Advantages of PDCA
- Easy to understand and apply across all organization types.
- Enables gradual and lasting improvements.
- Reduces risks associated with abrupt changes.
Limits of PDCA
- May be slow to deliver significant results.
- Requires solid KPI tracking to be truly effective.
In Summary: Which Method Should You Choose?
Method | Best For… | Strenghts | Weaknesses |
---|---|---|---|
Kaizen | Ongoing small improvements | Simple, engaging, effective long-term | Slow to deliver results |
Kanban | Tasks and process tracking | Visual, intuitive, improves workflow | Can become complex without structure |
Lean | Waste reduction | Resource optimization, cost savings | Can create pressure if misapplied |
Six Sigma | Defect reduction | Data-driven, quality enhancement | Heavy and complex method |
PDCA | Progressive improvements | Structured, effective for testing | Can be slow |
Continuous Improvement Software: Solutions for Teams and Individuals
Continuous improvement methods are powerful, but without the right tools, implementation can become a real headache. Thankfully, many software solutions are designed to support organizations in this endeavor, from idea management to process analysis and real-time tracking.
Here’s a roundup of the top continuous improvement tools!
Perfect for teams looking to structure and track their improvement processes, Asana is primarily a project management tool but adapts well to continuous improvement with task tracking, collaboration, and automation features.
What we like
- Clear and intuitive interface.
- Process tracking via list, Kanban board, or calendar.
- Automates repetitive tasks.
Limitations
- Limited analysis and reporting features.
- Less suited to companies with complex processes.
Pricing
- Free version with basic features.
- Premium from €10.99 / $10.99 / £9.49 per user per month.
ClickUp is a true Swiss army knife for organizing, tracking, and analyzing continuous improvement. It allows for custom dashboards, goal management, and workflow automation.
What we like
- Extreme customization of boards and workflows.
- Task management with over 15 views (Kanban, Gantt, List…).
- Advanced process automation.
Limitations
- Steep learning curve.
- Too many options may overwhelm users.
Pricing
- Free version with limited features.
- Paid plans from $7 per user per month.
KPI Fire is designed for managers and decision-makers who want real-time tracking of continuous improvement initiatives. It features analytical dashboards, an idea funnel, and key KPI monitoring.
What we like
- Aligns improvement goals with corporate strategy.
- Excellent idea and project tracking.
- Collaborative tool suited for large teams.
Limitations
- Outdated and basic interface.
- Non-transparent pricing.
Pricing
- Available upon request from KPI Fire.
Process Street is a workflow management tool that helps create and automate checklists, procedures, and recurring tasks. It’s especially useful for structuring continuous improvement processes and avoiding oversights.
What we like
- Easy drag & drop interface.
- Advanced automation without coding.
- Integrates with Slack, Zapier, Trello, and more.
Limitations
- High cost for small teams.
- Limited data analysis features.
Pricing
- Basic plan at $1,000 per year.
Software Comparison Summary
Software | Best For… | Strenghts | Weaknesses | Pricing |
---|---|---|---|---|
Asana | Task and process tracking | Simple, intuitive, flexible | Limited analysis features | Free / €10.99 / $10.99 / £9.49 per month |
ClickUp | Highly flexible organization and tracking | Highly customizable, many views | Complex for beginners | Free / $7 per month |
KPI Fire | KPI and improvement goal management | Advanced project tracking, idea management | Outdated interface | On request |
Process Street | Process automation | Easy to use, strong integrations | Expensive | $1,000 per year |
Yumana: A Collaborative Tool for Continuous Improvement
After reviewing several continuous improvement software options, it’s time to explore Yumana, a platform that stands out for its focus on collective intelligence. Unlike traditional tools centered around task or KPI management, Yumana emphasizes collaboration and team engagement to identify and scale the best improvement practices.
This approach directly boosts operational excellence by streamlining work processes and reducing inefficiencies!
Rather than enforcing top-down change, the platform enables every employee to submit local initiatives or adopt best practices implemented by other departments. By capitalizing on proven practices, companies can rapidly improve performance without reinventing the wheel. As a result, it fosters a far more effective and sustainable continuous improvement dynamic.
Key Features
One of Yumana’s strengths lies in its ability to centralize and structure continuous improvement initiatives.
No more juggling between Excel files and endless meetings, everything is gathered and tracked on a single interface.
The platform also includes gamification features to encourage contributions. Employees can like initiatives, experts can assess scalability potential, and managers can track deployment across different teams. This system helps build a true culture of continuous improvement and maintains long-term engagement.
Yumana is above all a community tool, allowing companies to build networks of operational performance leaders. These champions can be activated to support teams in deploying practices and solving identified issues.
It also provides ROI tracking through analytical dashboards. Companies can measure the impact of large-scale initiatives and adjust actions based on results.
Why Choose Yumana?
Unlike other tools focused on tasks and metrics, Yumana takes a more holistic and participative approach. It not only collects and structures best practices but also engages all teams in a dynamic and engaging improvement process.
While many tools remain locked in a top-down approach, the platform empowers employees by involving them directly in the process.
Companies that adopt it deploy best practices six times faster on the ground, significantly increasing ROI.
How to Implement it?
Implementation occurs in several stages. The first is defining continuous improvement goals and configuring the platform based on company-specific needs. Next comes a training and support phase to ensure quick adoption by teams.
Once the platform is up and running, employees can start submitting or adopting initiatives. The intuitive interface allows everyone to participate easily, with no technical skills required.
Try Yumana Today
The best way to experience Yumana’s potential is through a real-world trial.
The platform offers a demo so you can explore its features and evaluate how well it fits your organization’s specific needs.
By putting collective intelligence at the heart of continuous improvement, Yumana turns every employee into a change agent, helping companies stay competitive in an ever-changing environment.
Find out more about Continuous Improvement Tools…
- “Continuous Improvement Implementation Models” International Journal of Production Research, (2021).
- “Creating a Culture of Continuous Improvement” Aravind Chandrasekaran & John S. Toussaint – Harvard Business Review, (2019).
- “Continuous Improvement Through Lean Tools: An Application in a Manufacturing Company” Procedia Manufacturing, (2017).
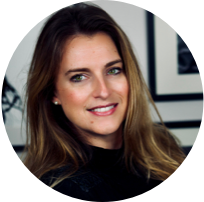
CEO & Co-Founder Yumana